Unmasking the Secrets: How to Detect Electric Motor Defects
In the world of machinery and industrial applications, electric motors play a crucial role in powering various operations. Ensuring that these motors are in pristine condition is vital for maintaining efficiency and preventing costly breakdowns. Motor reliability is a key factor that directly impacts the overall performance of equipment. Detecting defects within electric motors early on is essential to prevent potential issues from escalating. By unmasking the secrets behind identifying these defects, businesses can proactively address concerns and prolong the lifespan of their machinery.
Common Electric Motor Defects
Electric motors can experience a range of issues that impact their reliability and performance. One common defect is overheating, which can be caused by issues such as excessive friction, overloading, or high ambient temperatures. Overheating can result in insulation breakdown and winding damage, leading to motor failure.
Another prevalent issue is bearing failure, which can be caused by lack of lubrication, contamination, or misalignment. Worn-out bearings can lead to increased vibration and noise, ultimately affecting the overall efficiency and lifespan of the motor. Regular maintenance and monitoring of bearing conditions are crucial to prevent this issue.
Electrical faults, such as short circuits and open circuits, are also common in electric motors. These faults can occur due to factors like moisture ingress, insulation breakdown, or loose connections. Detecting and repairing electrical faults promptly is essential to prevent further damage and ensure the safe operation of the motor.
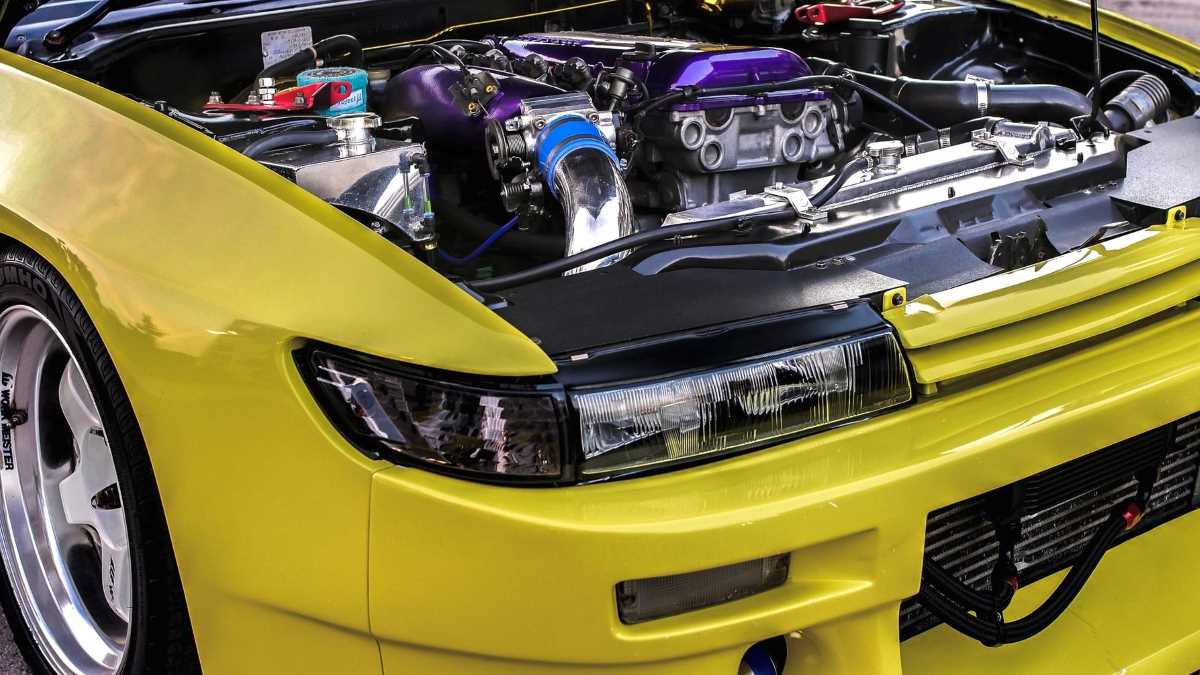
Advanced Detection Techniques
In addition to visual inspection and vibration analysis, advanced detection techniques can greatly enhance the reliability of electric motor performance. One such technique is infrared thermography, which involves capturing thermal images of the motor to detect potential hot spots that indicate internal faults or insulation degradation.
Another valuable method is motor current signature analysis, where electrical signals are analyzed to identify specific patterns associated with different types of motor defects. By monitoring and analyzing the motor's current signature, technicians can pinpoint abnormalities early on and take proactive measures to prevent further damage.
Furthermore, the use of online monitoring systems allows for continuous real-time tracking of motor performance parameters. These systems can provide valuable data on operating conditions, load fluctuations, and potential issues, enabling timely intervention and predictive maintenance strategies to ensure optimal motor reliability .
Ensuring Motor Reliability
When it comes to ensuring motor reliability, regular maintenance plays a crucial role in detecting potential defects before they escalate. By conducting routine inspections and testing, technicians can identify issues early on and prevent costly breakdowns. Implementing a proactive maintenance schedule can significantly increase the lifespan of electric motors.
Another key factor in ensuring motor reliability is monitoring operating conditions closely. By keeping track of factors such as temperature, vibrations, and load fluctuations, operators can detect abnormalities that may indicate underlying defects. Utilizing advanced monitoring tools and technologies can provide real-time data to help identify any potential issues and take corrective actions promptly.
In addition to maintenance and monitoring, investing in high-quality components and materials for electric motors is essential for ensuring long-term reliability. Using genuine parts and following manufacturer guidelines for repairs and replacements can help prevent defects and optimize the performance of motors. By prioritizing quality in every aspect of motor maintenance, reliability can be maximized to keep operations running smoothly.